1· 工程概况
嘉悦广场位于绍兴市柯桥群贤路与湖西路交叉口东北角的瓜渚湖畔,南临群贤路,工程总建筑面积104 228. 96 m2,地下2 层,建筑面积29 516 m2 ; 地上由一幢41 层超高层住宅、一幢4 层商业区及一幢10 层希尔顿酒店组成,建筑面积74 712. 96 m2。该工程主楼超高层为核心筒钢筋混凝土( 芯柱) 结构,建筑高度172 m; 4 层和10 层附楼为框剪结构,建筑高度分别为21. 9、43. 5 m。
该工程商业区第4 层为希尔顿酒店配套的宴会大厅,其屋顶框架大梁有4 榀,全采用后张法有粘结预应力混凝土结构体系,预应力梁跨度22. 8 m,离空高度9. 12 m,梁截面500 mm × 1 700 mm,梁上部采用上翻式,屋面板厚120 mm。
2 ·高支模体系设计与施工[1]
2. 1 技术难点分析
( 1) 高度高: 预应力屋面标高约22. 07 m,下部结构标高为12. 95 m,支模架高度9. 12 m。
( 2) 跨度大: 预应力梁最大跨度达22. 8 m,远远大于常规混凝土梁的跨度。见图1。
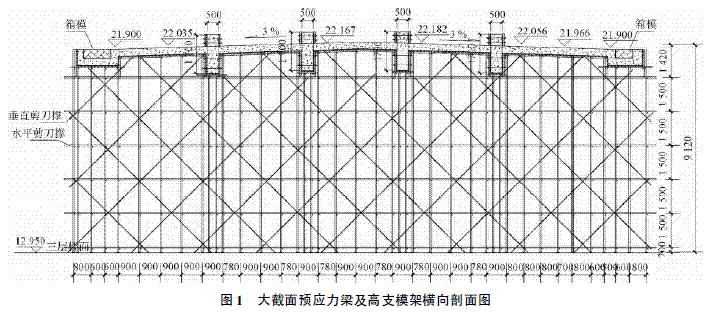
( 3) 截面大: 该工程商业区屋面4 榀梁截面为500 mm × 1 700 mm。见图2。
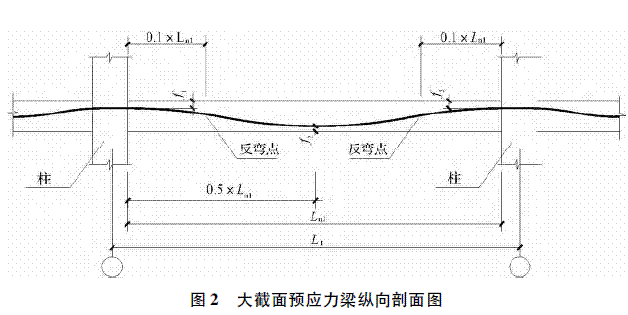
( 4) 荷载大: 预应力梁自重线荷载21. 25 kN/m,远大于15 kN/m,其模板支撑体系应具有足够的强度、刚度和稳定性,以确保屋面混凝土一次性浇筑成功。
2. 2 高支模体系选择
本工程屋面预应力梁空间高、跨度大、荷载大,危险性高,属于高支模体系,其支撑承重架的设计与施工尤为重要。鉴于近年来高支模架坍塌事故时有发生,尤其是引起的重特大安全事故发生率相应于其他原因引起的事故率高。其主要原因是,方案设计不合理,构造措施不符合稳定性要求,论证方案和实际施工不一致,施工现场管理混乱等。因此,本工程应单独编制安全专项施工方案并经专家论证审查。对高支模工程应遵循先设计后施工,设计与之相适应的支撑结构体系,保证其有足够的强度、刚度和稳定性,切实做到: 支撑体系设计与施工方案科学合理,专项方案应专家论证,并严格按论证审查通过后的方案进行施工。
根据模板工程工艺水平,结合规范要求和现场条件,本工程屋面预应力梁板结构采用扣件式钢管脚手架支撑体系,在保障安全可靠的前提下,梁与板整体支撑体系应做到: 构造要求规范设置,保证整体稳定性; 立杆步距一致,便于统一搭设;立杆纵或横距一致,便于立杆有一侧纵横向水平杆件拉通设置。
2. 3 高支模体系设计
本工程模板支架搭设计算高度取9. 12 m,梁和板模板均采用16 mm 厚胶合板,规格为1 830 mm ×915 mm; 方木规格为60 mm × 80 mm; 支撑系统采用48 × 3. 0 mm 满堂钢管脚手架,现浇板下立杆间距900 mm × 900 mm; 梁( 500 mm × 1 700 mm) 侧模采用4 道M12 对拉螺栓固定,对拉螺栓水平间距900 mm; 支撑立杆沿梁宽方向,梁两侧立杆间距900 mm,梁底设5 道方木,梁底部增设2 根承重立杆; 沿梁跨方向,梁底立杆间距为900 mm; 横杆步距1. 5 m,梁底小横杆沿梁跨方向间距为450 mm;立杆落脚在标高为12. 95 m 的3 层楼板上,对应的下层承重支模架待屋面预应力梁板结构施工完成后再拆除,其3 层楼板承载力满足上部施工及结构荷载要求。见图3。
2. 4 高支模体系设计验算
本高支模支架验算采用品茗建筑施工安全设施计算软件进行支模架设计验算,验算内容主要包括: ( 1) 模板验算; ( 2) 主、次楞验算; ( 3) 支撑钢管验算; ( 4) 扣件抗滑验算; ( 5) 立杆验算。按规范经验算复核,并经专家论证,本高支模体系符合要求。
2. 5 高支模体系构造措施
( 1) 双向设置扫地杆,在立杆底距地面200 mm高处,沿纵横水平方向按纵下横上的方式全设扫地杆。
( 2) 按步距双向满设水平杆,水平杆保证在同一条水平线上,确保两方向足够的设计刚度。
( 3) 梁底模处支撑横杆和立杆搭接采用双扣件连接,防止单个扣件失效导致排架整体破坏,所有立杆接长严禁搭接,须采用对接扣件连接,相邻两立杆的对接接头不得在同步内,且对接接头沿竖向错开的距离不宜小于500 mm,各接头中心距主节点不宜大于步距的1 /3。
( 4) 预应力大梁两侧沿全高各设一道竖向剪刀撑; 模板支架四边全高满布竖向剪刀撑,中间每隔4 排立杆设置一道纵、横向竖向剪刀撑,由底至顶全高连续设置; 模板支架四边与中间每隔4 排立杆从顶层开始向下每隔2 步设置一道水平剪刀撑; 剪刀撑搭接长度不小于1 000 mm,用3 个扣件扣牢。
( 5) 满堂架尽量与周边已浇筑的剪力墙或柱立体连接,增加模板支撑架的整体刚度,减少安全隐患。
3 ·预应力施工
3. 1 预应力梁施工工艺流程
预应力梁施工工艺流程如下: 高支模搭设→安装预应力梁底模→绑扎普通钢筋→埋设波纹管→穿钢绞线→锚具垫板安装→设置灌浆孔、排气孔→混凝土浇注→拆侧模→预应力筋张拉→孔道灌浆→锚具保护→高支模拆除。
3. 2 施工过程中应注意的问题
3. 2. 1 施工准备
针对预应力梁施工的具体要求,编制预应力梁施工专项方案,进行技术交底,保证超高、大跨度、大截面预应力梁施工质量。
3. 2. 2 材料和设备的检验
预应力钢筋全部采用Ⅱ级低松驰15. 24 钢绞线,抗拉强度标准值为fptk = 1 860 MPa,预应力孔道采用内径Φ70 mm 金属圆形波纹管,预应力梁混凝土强度等级为C40,孔道灌浆用42. 5 级硅酸盐水泥。
张 拉端与固定端锚具采用OAM15-2 夹片锚具和OVM15-P 型挤压式锚具,张拉采用ZB500 油泵,YCW1500 穿心式千斤顶进行张拉。
按规范标准,对材料检测和设备校验、标定,使用满足要求的材料、设备,确保预应力梁施工质量。
3. 2. 3 施工操作
( 1) 高大支模架搭设、监测、拆除。步骤如下:
①施工前,编制超高、大跨度、大截面梁板支模架专项方案,组织专家论证; 施工中,严格按专家论证的专项方案进行高支模架的搭设、拆除,确保高支模体系施工安全。②本工程高大支模架监测点采取在临边位置的柱、墙和钢管支模架上设置水平位移观测点和沉降位移观察点,并涂红漆作为监测标记,实时监测。在浇筑混凝土过程中监测频率每30 min 一次,终凝后监测频率为每天一次,连续观察7 d。
( 2) 孔道留设及预应力筋的穿放。由于预应力筋对构件截面引起的应力分布,与预应力筋的埋设位置有密切的关系,因此在施工中对孔道留设的位置要根据设计要求进行严格控制。
①本工程采用预埋波纹管的方法预留孔道,主要步骤如下:
a. 根据图纸计算波纹管及喇叭口的定位坐标数据,在单侧模板上标出预埋波纹管及喇叭口的位置,然后安装、校正并固定两端喇叭口;
b. 波纹管定位筋严格按间距800 mm 进行固定,为准确控制每一根定位筋的位置,施工中采用刻度定位法,即按照设计图给出的钢绞线的位置,画出定位筋的位置,再将定位筋焊接在上下排的受力钢筋上,这样就可以有效地保证定位筋的准确性。用20# ~ 22#铅丝将波纹管与定位筋绑扎牢固,防止波纹管在施工中产生移位和上浮;
c. 认真检查、校对波纹管的位置并最后固定金属波纹管;
d. 套管两端用防水胶布缠裹,宽度不小于50 mm;
e. 金属波纹管安装校正完毕后,用清孔器对波纹管进行清孔,如发现受阻,随时排除故障。
②将编好的钢绞线放在地面盘成圆盘,吊至楼面拆去绑扎铅丝,摊平放置在楼面处待穿。穿钢绞线前先用专用“护套”包住钢绞线端头,用机械配合人力,将钢绞线由固定端逐步穿至张拉端。
( 3) 本工程预应力结构体系由于高度较高,柱、梁和楼板混凝土分二次浇筑,所有竖向结构的框架柱先浇筑,水平结构的梁和屋面板混凝土后整体浇筑,并尽可能均匀对称浇筑,以防止高支模坍塌,在浇筑混凝土时还应做到:
①预应力大梁混凝土浇筑时,从大梁两侧向中间对称、均匀地分层浇筑,每层厚度不得大于400 mm,以确保高支撑架体受力均匀,防止架体整体失稳,从而保证高支撑架施工安全。
②严禁用振动棒振及波纹管,尤其在梁的端部及钢筋密集处宜采用小直径高频振动棒,以避免振动棒直接碰及波纹管; 对波纹管下部的混凝土必须振捣密实后再覆盖面层混凝土。
③为防止混凝土浇捣时漏入波纹管内,以及振捣时可能损坏波纹管形成堵塞,在混凝土初凝前应经常抽动钢绞线,确保孔道畅通。
④浇筑混凝土的同时制作混凝土试块,浇筑完毕待混凝土终凝后认真做好混凝土养护工作。
( 4) 混凝土养护28 d 后进行预应力筋张拉[2],钢绞线的张拉顺序要严格按设计要求进行。
①张拉力的控制。本工程预应力筋采用一端张拉的方法,张拉控制应力σcon = 0. 75fptk = 1 395 MPa。为弥补预应力损失,采用超张拉,经设计认可后,施工时张拉力提高了三个百分点。张拉方法根据设计要求为: 0→初应力( 100 kN) →1. 03σcon,然后锚固。
②张拉设备操作。将预应力筋穿入千斤顶的中心孔道中,在张拉油缸的端部用工具锚锚固,随后进行张拉。整个张拉过程中,千斤顶行程不得超过180 mm; 千斤顶油压不得超过最大张拉油压; 千斤顶张拉油缸进油时,回程油缸及液控顶压器必须处于回油状态; 千斤顶的回程油缸进油时,张拉油缸必须处于回油状态; 顶压过程中密切留意张拉油路升压情况,不得超过2 MPa。
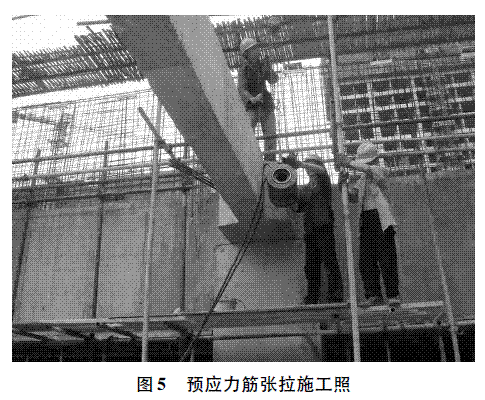
( 5) 孔道灌浆。①压浆前用压力水冲洗孔道,并清净积水,保证孔道压浆流畅,使浆液与孔壁结合良好,对排气孔、压浆孔、压浆设备等进行检查。
②孔道灌浆用42. 5 级硅酸盐水泥,水泥浆水灰比为0. 4 ~ 0. 45,计量准确,严格控制水灰比。水泥浆中加入减水剂,灌浆用水须清洁水。自调制至灌入孔道的延续时间,不超过45 min,且在使用前和压注过程中经常搅动。
③鉴于22. 8 m 预应力梁孔道较长,且采用波纹管成孔,考虑仅压注一次,水泥浆如有泌水和凝结收缩,会使孔道上部产生空隙,所以,为了保证有粘结预应力梁灌浆密实,对孔道进行二次压浆,二次压浆的间隔时间以先压注的水泥浆充分泌水又未初凝为宜[3]。
④压浆应缓慢、均匀地进行,不能连续压浆时,后压的孔道应在压浆前用压力水冲洗通畅。灌浆在梁端的灌浆口进行,采用二次灌浆的方法: 用灌浆机加压到0. 3 ~ 0. 4 MPa 将水泥浆压入孔道,待另一端排气孔流出浓水泥浆后,封闭排气孔; 二次继续加压至0. 6 ~ 0. 8 MPa,待压力达到后进行封堵。
⑤金属波纹管一旦破损产生漏浆,易造成孔道堵塞。施工中,精心施工、仔细检查,防止孔道内部漏浆凝固造成孔道堵塞,确保预应力孔道畅通。
⑥预应力筋全部张拉完毕后尽快灌浆,并在48 h 内完成。
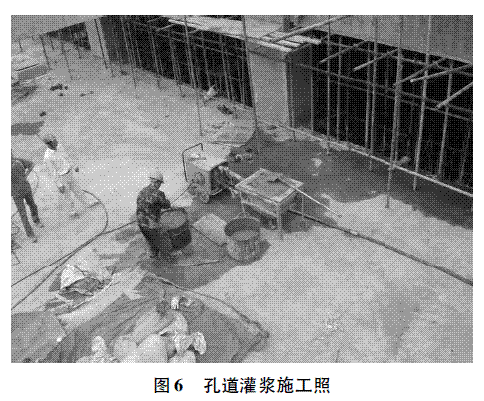
( 6) 锚具保护。灌浆完成后,可切割工作长度内多余钢绞线,露出锚具外的钢绞线不小于30 mm,外露预应力筋涂环氧树脂,并罩上封端塑料套,用微膨胀细石混凝土全封闭。
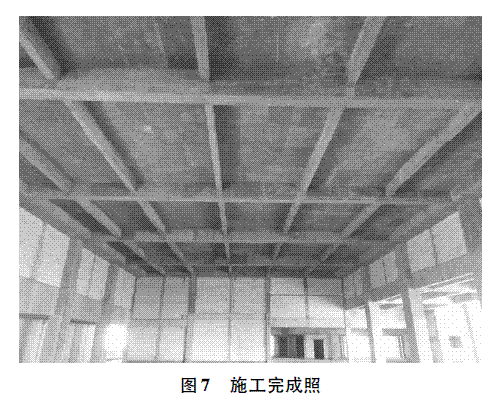
嘉悦广场位于绍兴市柯桥群贤路与湖西路交叉口东北角的瓜渚湖畔,南临群贤路,工程总建筑面积104 228. 96 m2,地下2 层,建筑面积29 516 m2 ; 地上由一幢41 层超高层住宅、一幢4 层商业区及一幢10 层希尔顿酒店组成,建筑面积74 712. 96 m2。该工程主楼超高层为核心筒钢筋混凝土( 芯柱) 结构,建筑高度172 m; 4 层和10 层附楼为框剪结构,建筑高度分别为21. 9、43. 5 m。
该工程商业区第4 层为希尔顿酒店配套的宴会大厅,其屋顶框架大梁有4 榀,全采用后张法有粘结预应力混凝土结构体系,预应力梁跨度22. 8 m,离空高度9. 12 m,梁截面500 mm × 1 700 mm,梁上部采用上翻式,屋面板厚120 mm。
2 ·高支模体系设计与施工[1]
2. 1 技术难点分析
( 1) 高度高: 预应力屋面标高约22. 07 m,下部结构标高为12. 95 m,支模架高度9. 12 m。
( 2) 跨度大: 预应力梁最大跨度达22. 8 m,远远大于常规混凝土梁的跨度。见图1。
( 3) 截面大: 该工程商业区屋面4 榀梁截面为500 mm × 1 700 mm。见图2。
( 4) 荷载大: 预应力梁自重线荷载21. 25 kN/m,远大于15 kN/m,其模板支撑体系应具有足够的强度、刚度和稳定性,以确保屋面混凝土一次性浇筑成功。
2. 2 高支模体系选择
本工程屋面预应力梁空间高、跨度大、荷载大,危险性高,属于高支模体系,其支撑承重架的设计与施工尤为重要。鉴于近年来高支模架坍塌事故时有发生,尤其是引起的重特大安全事故发生率相应于其他原因引起的事故率高。其主要原因是,方案设计不合理,构造措施不符合稳定性要求,论证方案和实际施工不一致,施工现场管理混乱等。因此,本工程应单独编制安全专项施工方案并经专家论证审查。对高支模工程应遵循先设计后施工,设计与之相适应的支撑结构体系,保证其有足够的强度、刚度和稳定性,切实做到: 支撑体系设计与施工方案科学合理,专项方案应专家论证,并严格按论证审查通过后的方案进行施工。
根据模板工程工艺水平,结合规范要求和现场条件,本工程屋面预应力梁板结构采用扣件式钢管脚手架支撑体系,在保障安全可靠的前提下,梁与板整体支撑体系应做到: 构造要求规范设置,保证整体稳定性; 立杆步距一致,便于统一搭设;立杆纵或横距一致,便于立杆有一侧纵横向水平杆件拉通设置。
2. 3 高支模体系设计
本工程模板支架搭设计算高度取9. 12 m,梁和板模板均采用16 mm 厚胶合板,规格为1 830 mm ×915 mm; 方木规格为60 mm × 80 mm; 支撑系统采用48 × 3. 0 mm 满堂钢管脚手架,现浇板下立杆间距900 mm × 900 mm; 梁( 500 mm × 1 700 mm) 侧模采用4 道M12 对拉螺栓固定,对拉螺栓水平间距900 mm; 支撑立杆沿梁宽方向,梁两侧立杆间距900 mm,梁底设5 道方木,梁底部增设2 根承重立杆; 沿梁跨方向,梁底立杆间距为900 mm; 横杆步距1. 5 m,梁底小横杆沿梁跨方向间距为450 mm;立杆落脚在标高为12. 95 m 的3 层楼板上,对应的下层承重支模架待屋面预应力梁板结构施工完成后再拆除,其3 层楼板承载力满足上部施工及结构荷载要求。见图3。
2. 4 高支模体系设计验算
本高支模支架验算采用品茗建筑施工安全设施计算软件进行支模架设计验算,验算内容主要包括: ( 1) 模板验算; ( 2) 主、次楞验算; ( 3) 支撑钢管验算; ( 4) 扣件抗滑验算; ( 5) 立杆验算。按规范经验算复核,并经专家论证,本高支模体系符合要求。
2. 5 高支模体系构造措施
( 1) 双向设置扫地杆,在立杆底距地面200 mm高处,沿纵横水平方向按纵下横上的方式全设扫地杆。
( 2) 按步距双向满设水平杆,水平杆保证在同一条水平线上,确保两方向足够的设计刚度。
( 3) 梁底模处支撑横杆和立杆搭接采用双扣件连接,防止单个扣件失效导致排架整体破坏,所有立杆接长严禁搭接,须采用对接扣件连接,相邻两立杆的对接接头不得在同步内,且对接接头沿竖向错开的距离不宜小于500 mm,各接头中心距主节点不宜大于步距的1 /3。
( 4) 预应力大梁两侧沿全高各设一道竖向剪刀撑; 模板支架四边全高满布竖向剪刀撑,中间每隔4 排立杆设置一道纵、横向竖向剪刀撑,由底至顶全高连续设置; 模板支架四边与中间每隔4 排立杆从顶层开始向下每隔2 步设置一道水平剪刀撑; 剪刀撑搭接长度不小于1 000 mm,用3 个扣件扣牢。
( 5) 满堂架尽量与周边已浇筑的剪力墙或柱立体连接,增加模板支撑架的整体刚度,减少安全隐患。
3 ·预应力施工
3. 1 预应力梁施工工艺流程
预应力梁施工工艺流程如下: 高支模搭设→安装预应力梁底模→绑扎普通钢筋→埋设波纹管→穿钢绞线→锚具垫板安装→设置灌浆孔、排气孔→混凝土浇注→拆侧模→预应力筋张拉→孔道灌浆→锚具保护→高支模拆除。
3. 2 施工过程中应注意的问题
3. 2. 1 施工准备
针对预应力梁施工的具体要求,编制预应力梁施工专项方案,进行技术交底,保证超高、大跨度、大截面预应力梁施工质量。
3. 2. 2 材料和设备的检验
预应力钢筋全部采用Ⅱ级低松驰15. 24 钢绞线,抗拉强度标准值为fptk = 1 860 MPa,预应力孔道采用内径Φ70 mm 金属圆形波纹管,预应力梁混凝土强度等级为C40,孔道灌浆用42. 5 级硅酸盐水泥。
张 拉端与固定端锚具采用OAM15-2 夹片锚具和OVM15-P 型挤压式锚具,张拉采用ZB500 油泵,YCW1500 穿心式千斤顶进行张拉。
按规范标准,对材料检测和设备校验、标定,使用满足要求的材料、设备,确保预应力梁施工质量。
3. 2. 3 施工操作
( 1) 高大支模架搭设、监测、拆除。步骤如下:
①施工前,编制超高、大跨度、大截面梁板支模架专项方案,组织专家论证; 施工中,严格按专家论证的专项方案进行高支模架的搭设、拆除,确保高支模体系施工安全。②本工程高大支模架监测点采取在临边位置的柱、墙和钢管支模架上设置水平位移观测点和沉降位移观察点,并涂红漆作为监测标记,实时监测。在浇筑混凝土过程中监测频率每30 min 一次,终凝后监测频率为每天一次,连续观察7 d。
( 2) 孔道留设及预应力筋的穿放。由于预应力筋对构件截面引起的应力分布,与预应力筋的埋设位置有密切的关系,因此在施工中对孔道留设的位置要根据设计要求进行严格控制。
①本工程采用预埋波纹管的方法预留孔道,主要步骤如下:
a. 根据图纸计算波纹管及喇叭口的定位坐标数据,在单侧模板上标出预埋波纹管及喇叭口的位置,然后安装、校正并固定两端喇叭口;
b. 波纹管定位筋严格按间距800 mm 进行固定,为准确控制每一根定位筋的位置,施工中采用刻度定位法,即按照设计图给出的钢绞线的位置,画出定位筋的位置,再将定位筋焊接在上下排的受力钢筋上,这样就可以有效地保证定位筋的准确性。用20# ~ 22#铅丝将波纹管与定位筋绑扎牢固,防止波纹管在施工中产生移位和上浮;
c. 认真检查、校对波纹管的位置并最后固定金属波纹管;
d. 套管两端用防水胶布缠裹,宽度不小于50 mm;
e. 金属波纹管安装校正完毕后,用清孔器对波纹管进行清孔,如发现受阻,随时排除故障。
②将编好的钢绞线放在地面盘成圆盘,吊至楼面拆去绑扎铅丝,摊平放置在楼面处待穿。穿钢绞线前先用专用“护套”包住钢绞线端头,用机械配合人力,将钢绞线由固定端逐步穿至张拉端。
( 3) 本工程预应力结构体系由于高度较高,柱、梁和楼板混凝土分二次浇筑,所有竖向结构的框架柱先浇筑,水平结构的梁和屋面板混凝土后整体浇筑,并尽可能均匀对称浇筑,以防止高支模坍塌,在浇筑混凝土时还应做到:
①预应力大梁混凝土浇筑时,从大梁两侧向中间对称、均匀地分层浇筑,每层厚度不得大于400 mm,以确保高支撑架体受力均匀,防止架体整体失稳,从而保证高支撑架施工安全。
②严禁用振动棒振及波纹管,尤其在梁的端部及钢筋密集处宜采用小直径高频振动棒,以避免振动棒直接碰及波纹管; 对波纹管下部的混凝土必须振捣密实后再覆盖面层混凝土。
③为防止混凝土浇捣时漏入波纹管内,以及振捣时可能损坏波纹管形成堵塞,在混凝土初凝前应经常抽动钢绞线,确保孔道畅通。
④浇筑混凝土的同时制作混凝土试块,浇筑完毕待混凝土终凝后认真做好混凝土养护工作。
( 4) 混凝土养护28 d 后进行预应力筋张拉[2],钢绞线的张拉顺序要严格按设计要求进行。
①张拉力的控制。本工程预应力筋采用一端张拉的方法,张拉控制应力σcon = 0. 75fptk = 1 395 MPa。为弥补预应力损失,采用超张拉,经设计认可后,施工时张拉力提高了三个百分点。张拉方法根据设计要求为: 0→初应力( 100 kN) →1. 03σcon,然后锚固。
②张拉设备操作。将预应力筋穿入千斤顶的中心孔道中,在张拉油缸的端部用工具锚锚固,随后进行张拉。整个张拉过程中,千斤顶行程不得超过180 mm; 千斤顶油压不得超过最大张拉油压; 千斤顶张拉油缸进油时,回程油缸及液控顶压器必须处于回油状态; 千斤顶的回程油缸进油时,张拉油缸必须处于回油状态; 顶压过程中密切留意张拉油路升压情况,不得超过2 MPa。
( 5) 孔道灌浆。①压浆前用压力水冲洗孔道,并清净积水,保证孔道压浆流畅,使浆液与孔壁结合良好,对排气孔、压浆孔、压浆设备等进行检查。
②孔道灌浆用42. 5 级硅酸盐水泥,水泥浆水灰比为0. 4 ~ 0. 45,计量准确,严格控制水灰比。水泥浆中加入减水剂,灌浆用水须清洁水。自调制至灌入孔道的延续时间,不超过45 min,且在使用前和压注过程中经常搅动。
③鉴于22. 8 m 预应力梁孔道较长,且采用波纹管成孔,考虑仅压注一次,水泥浆如有泌水和凝结收缩,会使孔道上部产生空隙,所以,为了保证有粘结预应力梁灌浆密实,对孔道进行二次压浆,二次压浆的间隔时间以先压注的水泥浆充分泌水又未初凝为宜[3]。
④压浆应缓慢、均匀地进行,不能连续压浆时,后压的孔道应在压浆前用压力水冲洗通畅。灌浆在梁端的灌浆口进行,采用二次灌浆的方法: 用灌浆机加压到0. 3 ~ 0. 4 MPa 将水泥浆压入孔道,待另一端排气孔流出浓水泥浆后,封闭排气孔; 二次继续加压至0. 6 ~ 0. 8 MPa,待压力达到后进行封堵。
⑤金属波纹管一旦破损产生漏浆,易造成孔道堵塞。施工中,精心施工、仔细检查,防止孔道内部漏浆凝固造成孔道堵塞,确保预应力孔道畅通。
⑥预应力筋全部张拉完毕后尽快灌浆,并在48 h 内完成。
( 6) 锚具保护。灌浆完成后,可切割工作长度内多余钢绞线,露出锚具外的钢绞线不小于30 mm,外露预应力筋涂环氧树脂,并罩上封端塑料套,用微膨胀细石混凝土全封闭。